Everything about our technology is designed with modularity at heart, bringing significant benefits in biosecurity, reliability, maintenance, and operational efficiency
In the first of a four-part series focusing on the unique benefits of IGS technology, our Head of Vertical Farming Solutions, Douglas Elder, speaks about how modularity enhances the grower experience. Douglas’ unique blend of engineering and detailed industry know-how has seen him play a pivotal role in our technology’s evolution since joining IGS in 2015.
Modularity in vertical farming brings many benefits. At IGS, we have designed our tech solutions with this principle at heart, making them easier to scale, maintain, and operate. This can be seen across many areas – from rolling out periodic and iterative updates and upgrades, to optimising individual Growth Towers to different crop needs and specifications.
Modular vertical farming technology brings a wealth of benefits to the grower across biosecurity, reliability and maintenance, as well as general operational efficiency in a working horticultural environment. These are all key areas where growers can realise significant improvements, whether that’s in the ability to minimise the risk of an outbreak of pests or disease, increase fire safety, or eliminate downtime in production during key maintenance periods.
Biosecurity
Biosecurity is fundamental to any successful vertical farming operation. It’s often seen as one of the major USPs of vertical farming as a whole, but if the technology doesn’t lend itself to it, you risk contamination across the whole site, and potentially catastrophic losses.
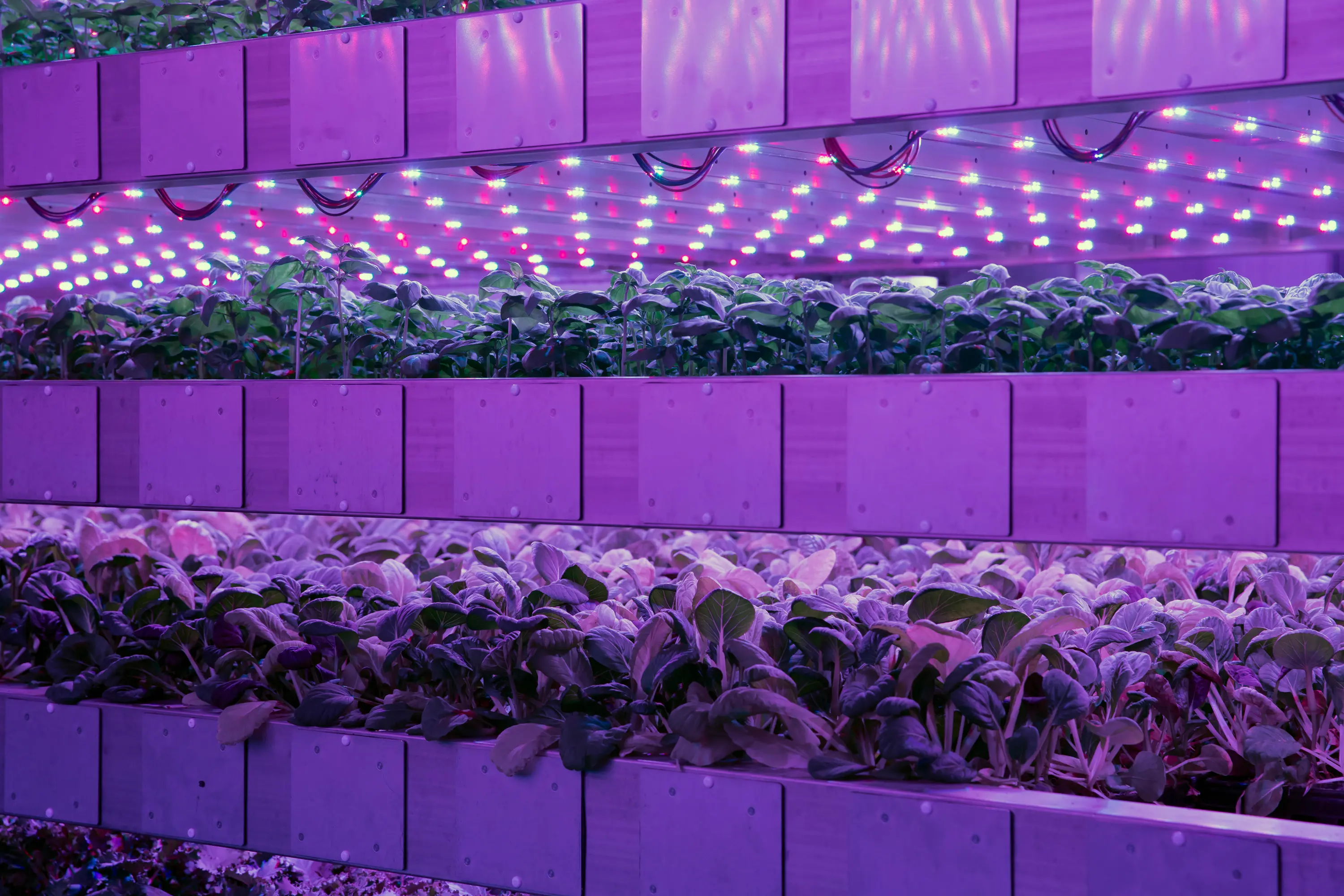
Tower and tray segregation
One of the core areas in which modularity shines through is in tower segregation. By separating each tower from its neighbour, we effectively reduce the risk area. This modularity is replicated across our systems, from Growth Trays with Lights (GTLs) in which crops are grown, through to the Growth Towers which house them, and the facility as a whole. Each Growth Tower has its own closed loop ventilation and fertigation systems which eliminate cross-tower contamination. The use of positive pressure airflow and segregated irrigation helps to limit any interaction between trays inside the Growth Tower, by working across as small an area as possible. This ensures that any potential outbreak can be contained and does not have a knock-on effect across the wider operation.
Cleaning
When working with plants, you’re always going to have to factor in cleaning. Normal crop cycles can range from seven days to three months, during which algae and biofilms can contaminate the growth environment. If left unchecked, this can lead to yield reductions over time. To avoid this, our Growth Trays use a modular design and can be completely removable as part of the normal growth cycle. They can be easily taken out and cleaned after every cycle, working to avoid wider disruption, reduce downtime, and deliver optimal yield outputs.
Facility design
Looking at the wider facility design, there are two key areas where modularity helps growers maintain biosecurity – the airlock, and the superstructure. An airlock plays a pivotal role in biosecurity by managing air movement across the whole facility, further enhancing the biosecurity of each Tower by keeping external air interactions to a minimum.
Our design ensures any air brought in from outside is HEPA filtered, removing dust and harmful pathogens. In turn, this reduces the load of that air into the towers, as we only replace the volume that can be contained in the airlock itself. The air within the Growth Tower is then recirculated through UV treatment, maintaining air quality. Another benefit of the airlock is that it effectively manages the movement of people. This means that people need to go through a controlled process to enter restricted areas, such as those where sowing or harvesting takes place. The superstructure is typically built from Structural Insulated Panels (SIPs). This well-established construction approach makes maintaining a high degree of air tightness easy. In combination with the airlock, this approach keeps pests and contamination out. The panels can also be coated with antibacterial surfaces, helping to reduce potential mould build-up and to establish easy-to-clean, food-safe surfaces in the growth environment. This enhances system hygiene, while also saving growers time and resources on site upkeep.
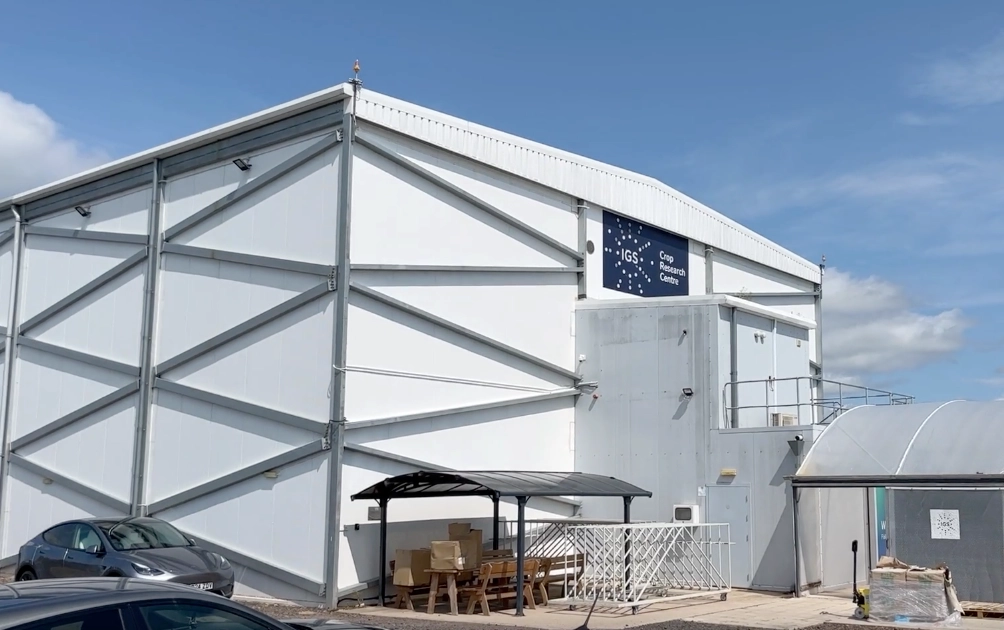
Minimising downtime
How modularity reduces downtime is critical. The design and its modular components mean that most of the time towers can remain operational even during deep cleaning. In a non-modular system, towers need to be regularly shut down to facilitate this, resulting in a loss of output and wider knock-on effects.
Downtime can be one of the biggest cost reducers for a vertical farm operation, so we stay on top of this by segregating everything from the individual trays and components through to the towers themselves. We’ll speak more about the benefits this brings during upgrades and developments, but in terms of biosecurity, modularity is so important as it allows growers to stay on top of system hygiene without affecting the wider operation.
Reliability and maintenance
We know that having modular components helps growers with general upkeep, as well as working with the product over a longer period. Modularity means that parts can be easily sourced when required, allowing for easier maintenance, while also helping with scalability. It then means that growers can integrate modular technology into a wider agricultural operation, combining new technologies with tried-and-tested ancillary components. This benefits customers in areas such as the heating, ventilation, and air conditioning (HVAC) system, all the way through to future-proofing the design when it comes to additions such as LED upgrades.
Balancing HVAC load
Like many elements of IGS’ technology, we’ve designed our HVAC system to be as energy efficient as possible, and modularity plays its part in helping this. We enable each Growth Tower to optimise its environment to suit the particular crop it is growing. Growers can then further optimise the environment to suit the growth stage within each Growth Tray. By deliberately positioning the crops at mixed stages throughout the tower and maintaining a constant production output (as opposed to batch production), we size our HVAC to the midpoint, rather than the peak. This drastically improves system efficiency. In a push-through system, this approach isn’t possible due to crops being clustered at the same stage of growth in one area. This then leads to hotspots, placing significant load on the HVAC load and making it difficult to maintain a consistent environment across the facility.
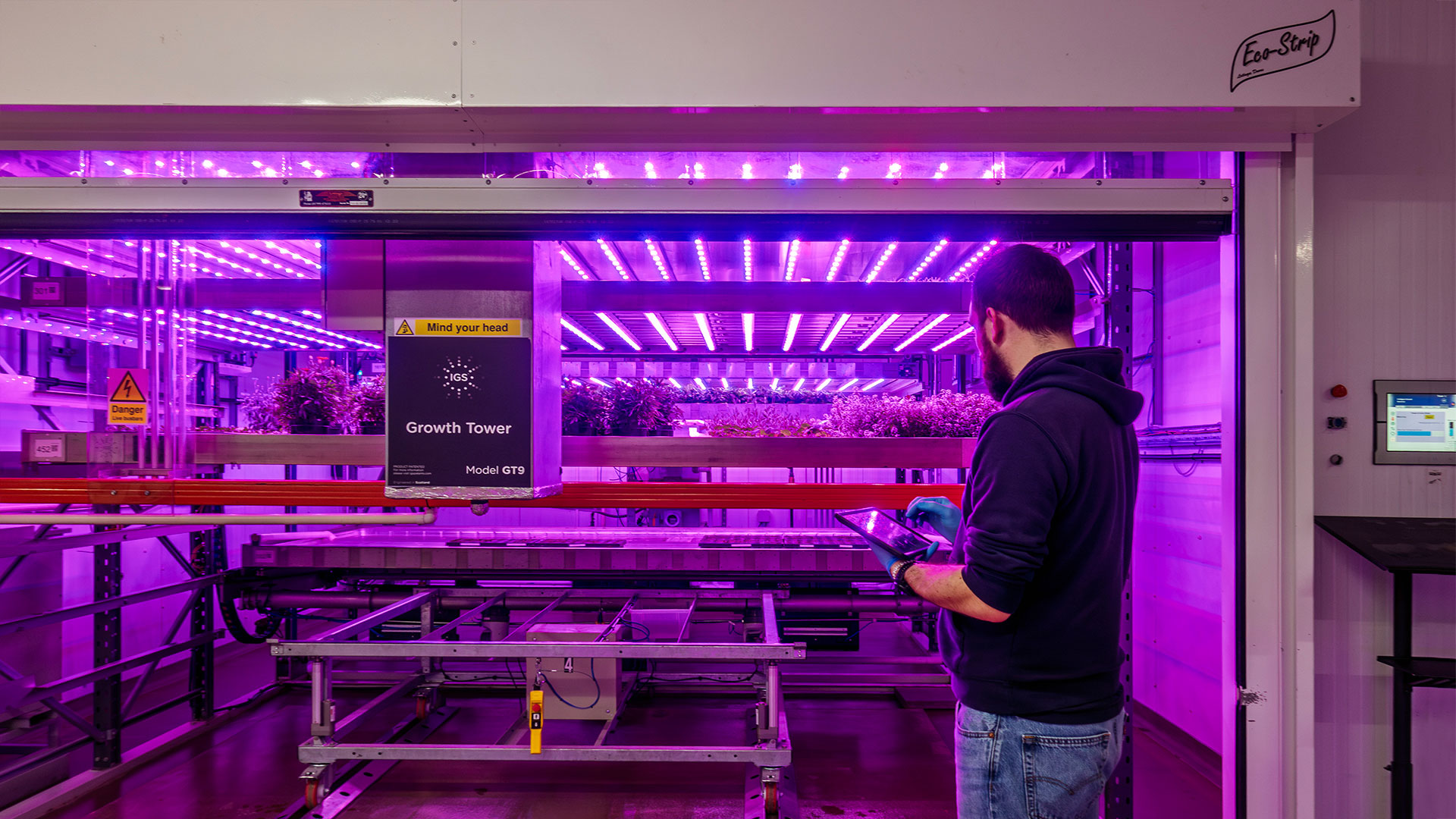
Operational safety
In an indoor growing environment, there’s always going to be a need for significant irrigation and areas of elevated humidity working alongside the necessary electronics used to maintain the environment. Combined, this can pose a significant fire risk, particularly as LED drivers age and begin to fail. This makes it important to put in place suitable safety measures, as there have been several examples in recent years where catastrophic fires have occurred in other vertical farming systems.
We use an extra low voltage system, which can reduce the capital cost by removing the need to IP-rate components. This has additional safety benefits by removing the electric shock risk for operators. Even in IP-rated components, the risk of electronic failure can lead to fire. We have factored this in by using metal tray liners, rather than polystyrene. This effectively eliminates the risk of fire caused by the combination of electrical equipment and water, while our modular design reinforces this by isolating potential hazards and keeping Growth Towers segregated. The ability to remove and maintain electronics outside of the Growth Tower also ensures that the need to work at height is reduced.
Future-proofing hardware
Another key advantage of modularity lies in futureproofing. LED lights will either need replacing at the end of their life cycle or upgrading when a newer version is rolled out. A modular system means that they can be replaced without a full system shutdown, allowing operations to continue and a consistent revenue stream to be in place.
This also means that growers can implement a phased transition, rolling out upgrades and spreading the cost over a period of time. You can essentially do it on a Growth Tray-by-Growth Tray basis, ensuring continuous improvement while maintaining operational efficiency. Electricians aren’t needed to perform these upgrades as the system is extra-low voltage, helping to significantly bring down costs.
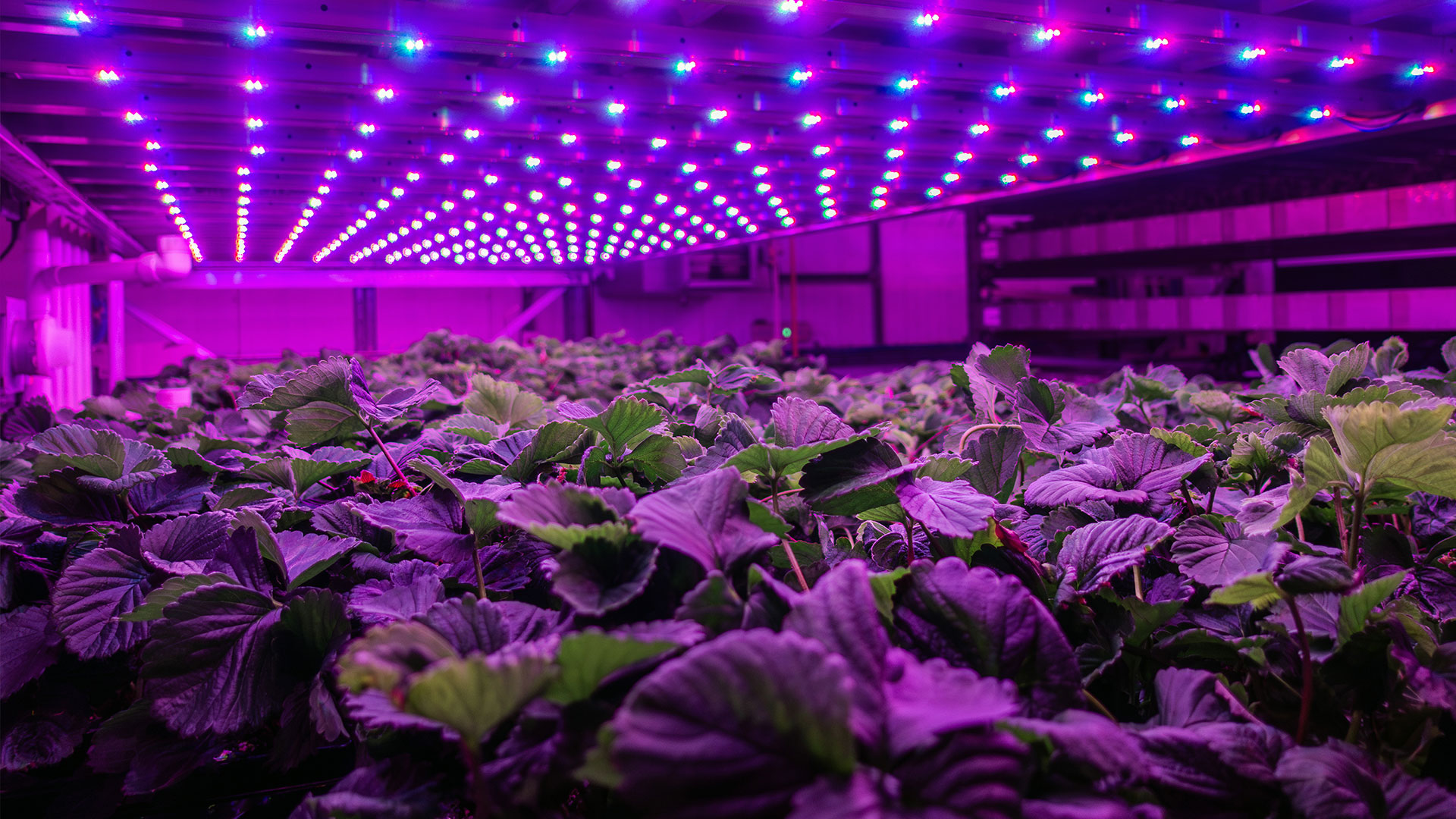
Operational efficiency
Besides the biosecurity and maintenance advantages, a modular system makes it easy for growers to embed efficient procedures across their operation. This is clear when looking at spatial elements, as well as how the system works during busy harvest times.
Reducing labour requirements and maximising the growing area
A modular design also allows the Growth Trays to be spaced closer together. This helps to optimise the overall space (as there is less space between trays), with individual trays placed as little as 250 millimetres apart. Space efficiency comes into its own here, growing a large number of crops in a relatively small area. We’ve designed our HVAC so that it can handle this level of work as a single system, as opposed to multiple different ones. On a tower level, you’re also able to do maintenance on one specific area without shutting down the wider facility. Again, this means that growers can continue operations throughout any deep-cleaning, maintenance, or upgrade exercises, and are able to limit overall human resource.
Reducing congestion during busy harvests
Having multiple towers made up of modular components allows growers to create so-called growing ‘zones’. These really come into their own during busy harvests. Instead of removing a full tower’s worth of trays at once, operations can be spread over a larger area (of multiple towers) allowing for smoother, batch processing. This reduces queues and means that the towers are working together to produce the same crop, at the same time, more efficiently. These zones can be adapted at any time to modify production needs according to market demand.
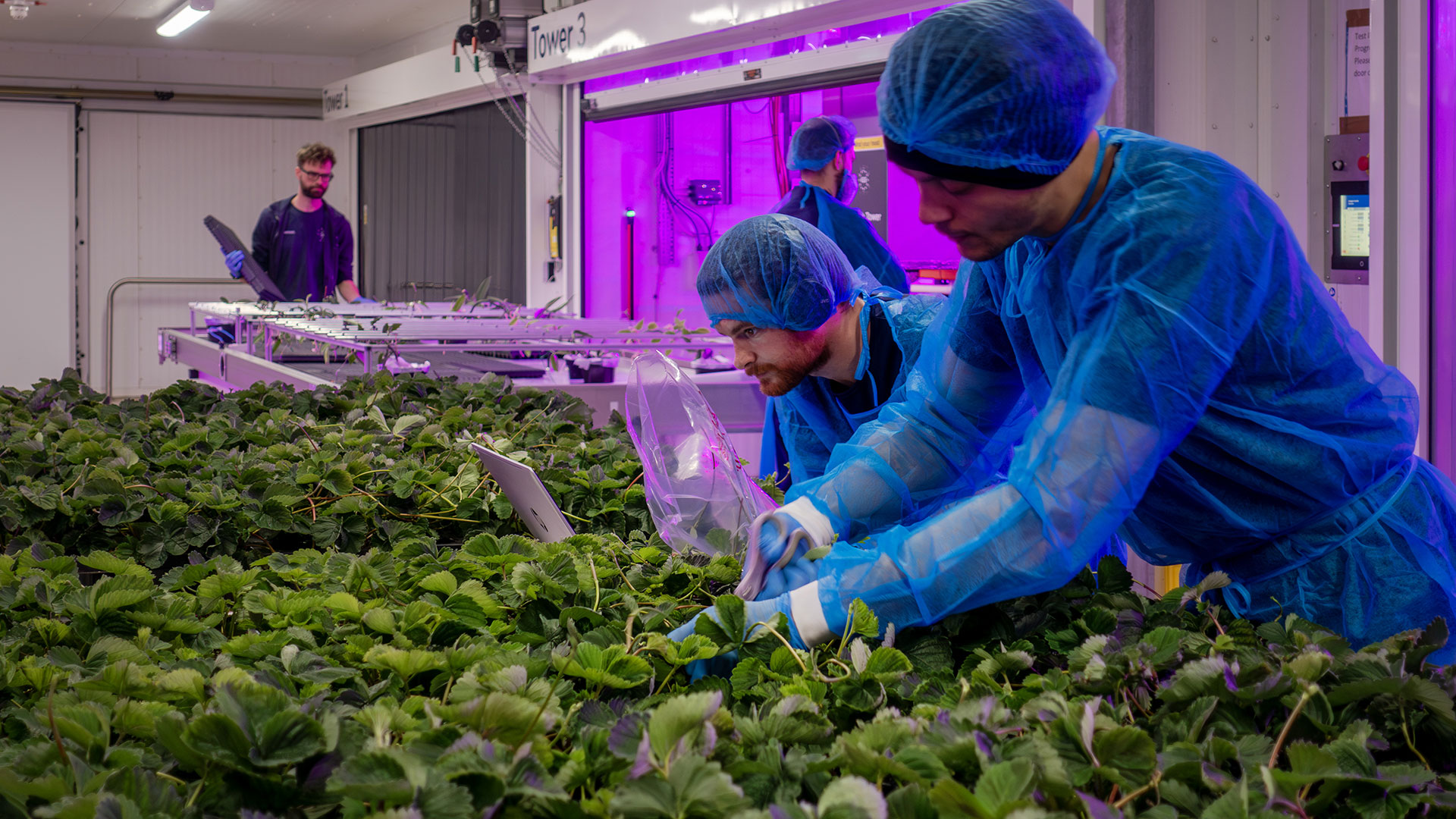
Benefit from iterative software upgrades
We supply our customers with iterative software upgrades to enhance the grower experience. A modular design means that these upgrades can be quickly tested and implemented without impacting plant production. Hardware upgrades can be retrofitted, ensuring compatibility between old and new versions, as the general interface remains modular and easy to integrate. In the future, specialised modules containing features such as enhanced lighting arrangements or sensing capabilities could be deployed and used in multiple locations within the facility, as opposed to having them fitted throughout. This helps to maintain system efficiency over time. It also works to help deliver innovative and necessary upgrades to both software and hardware, making sure the grower is well-equipped and working with the latest crop science.
Modularity in practice
Modularity is a key aspect of IGS technology. It plays a key role in bolstering biosecurity and operational efficiency, as well as future-proofing the system by allowing upgrades to be periodically rolled out. This benefits growers across the board, but we see the real benefits here in minimising downtime. Modularity allows growers to keep towers operational during cleaning, avoiding the need for regular full-site shutdowns and maintaining output levels. From a biosecurity, operational, and general maintenance perspective, this pays dividends, as it helps to maintain a consistent revenue stream, all while ensuring that relevant checks and upgrades are undertaken for overall tower health.
We like to think of modularity as just one of several ways our technology stands out among the crowd. Over the coming weeks, we’ll be covering how our tech solutions help customers flex to market demand, scale when need be, and embed real efficiencies which help over the long (and short) run.
Like what you’ve read? Look back at our blog for other articles on vertical farming.